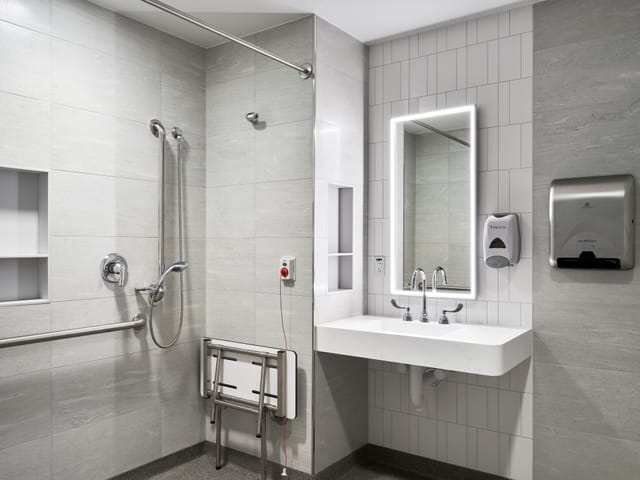
Atrium Health Carolinas Rehabilitation – (read more)
SurePods provided 72 patient bathroom pods for the 5-story Carolinas Rehabilitation Replacement Facility.
Resource Library
In response to the increasing demand for quality healthcare in Charlotte, North Carolina, Atrium Health, a leading healthcare facilitator, decided to expand its infrastructure to ensure the delivery of high-quality healthcare services in the fast-growing metropolitan area. The organization planned to build four facilities accommodating 500 licensed patient beds, including patient care and rehabilitation.
The building and design teams for these projects commissioned SurePods, North America’s leading factory-built bathroom pods producer, to craft modular bathroom pods for all four Atrium Health facilities. Together with Atrium Health, SurePods and the design teams created precise prefabricated bathroom units that benefited all stakeholders. Taking a standardized approach to design optimized capital, time, and available labor resources. The successful implementation of prefabricated bathroom pods showcases a significant shift in healthcare construction practices.
UNIFIED DESIGN STRATEGY BRINGS STANDARDIZATION TO DIVERSE PROJECTS
Despite varying timelines and teams, Atrium Health approached these four projects through the shared objective of standardization and achieving economies of scale using prefabricated elements. Considering patient-specific needs in each facility, different architecture and contracting firms were commissioned to execute under the shared single-standard approach.
For the Atrium Health Carolinas Rehabilitation replacement facility, design firm NBBJ joined forces with general contracting firm DPR Construction. DLR Group, an integrated design firm, collaborated with Rodgers Builders to bring the Atrium Health Pineville-Palmetto Tower to completion. Two additional Atrium Health projects remain in progress.
“Atrium Health believes prefabrication is the way of the future.”
Damian Huneycutt, Healthcare Client Leader and Principal at DLR Group, shared insights into the prefab decision-making process. “Atrium Health believes prefabrication is the way of the future,” he explained. “They told us they’d seen it done successfully, and although they had not yet utilized this approach, they wanted to start implementing prefabrication going forward.” Along with implementing a forward-thinking approach, Atrium Health wanted to optimize its capital investment by reducing the cost per unit.
“We went in with the intention to implement standardization and to bulk-buy,” Jeff Schroder, Atrium Health’s Assistant Vice President of Planning, Design and Construction said. “This led us to set a goal that about 60 percent of the project would be prefabricated.”
QUALITY AND CONSISTENCY WITH PREFABRICATED BATHROOM PODS
“Maintaining the same bathroom layout and patient room layout in every hospital was important so that staff could move easily between different Atrium Health locations,” Scott MacLeod, Project Director at DPR said. Opting for standardization in bathrooms “lets the nurses focus on being nurses,” according to Huneycutt.
Given that bathrooms are one of the most resource-intensive parts of a healthcare project—typically requiring 8-12 trade agencies like plumbing, electrical, painting, tiling and drywall to work in close proximity over a matter of weeks.
Prefabricating bathrooms off-site streamlines this process. It enables concurrent construction in a controlled environment while eliminating the complex coordination of trades and the risk of damage to previously finished work. It supports a lean construction process by addressing design issues and material availability upfront.
Eric Fix, the Vice President of Construction Operations at Rodgers Builders shared, “I think the architectural industry is coming around to accepting manufactured building components. They are now able to compare the quality and the consistency of a traditional method and that of a prefabricated one, especially when it comes to bathrooms.”
To deliver this promise, the building and design teams commissioned SurePods, North America’s leading factory-built bathroom pods producer, to craft modular bathroom units for all four Atrium Health facilities offsite. “We ultimately chose SurePods based on their quality, manufacturing reputation and ability to meet our production schedule,” Huneycutt said. “They were the best choice for the project.”
The collective design team, experts at SurePods, and technical representatives, collaborated to establish a basis for design. “Everyone was involved at an early stage to make this project successful, including the architects, engineers, contractors and other subcontractors,” Justin Elliot, the plumbing contractor on each of the Atrium Health projects explained.
Using the approved blueprint, the team at SurePods utilized building information modeling (BIM) software to create a 3D “digital twin” of the pods and build a sample prototype. After each design detail was physically inspected, SurePods mass-produced the bathroom pods to alleviate complexity in the design process. “The architects were designing the patient rooms around standardized bathroom layouts,” Schroder reported. "Even if there are small modifications in the bathroom configuration, the overall framework would still be the same. So, for the planner, the bathroom pod acts like a LEGO piece that just snaps into its designated place."
"Even if there are small modifications in the bathroom configuration, the overall framework would still be the same. So, for the planner, the bathroom pod acts like a LEGO piece that just snaps into its designated place."
After the pods are delivered to the project site, they are inspected at various stages. “We checked them when they arrived, when they were unwrapped, and then again before they were placed,” Fix said. “Utilizing SurePods really takes some of the most labor-intensive parts of construction and pulls all that work forward in the schedule.”
The involvement of many trades for site execution can typically mean repetitive quality checks and reworks in the construction process, which can strain the timeline on large-scale projects. The pressure is further exacerbated by the fact that bathroom reworks can account for about 60 percent of punch lists in most multi-unit projects. As such, long punch lists and changing hands leave room for quality errors.
Sidelining this problem, SurePods guarantees quality by manufacturing the pods in their facilities offsite. The controlled environments ensure consistency and minimize the number of agencies involved on-site. “So not only are you not cluttering up the job with all these loose little parts and pieces and the extra labor, but you also have a lower punch list at the end of the day,” Fix reported. “You finish quicker and easier without a lot of reworks at the end.”
STREAMLINING OPERATIONS THROUGH PREFABRICATION
As with many urban cities around the country, the pandemic heavily impacted the availability of skilled labor in Charlotte. While optimizing labor was not at the forefront of choosing standardization for the Atrium Health projects, “it became a great byproduct of prefabrication,” Schroder explained. “We were taking a lot of the labor off the job, which was a benefit because there’s just not enough labor in town.”
Mass manufacturing of the bathroom pods also aided the execution teams and skilled laborers hired to work on the Atrium Health projects. “If we had to focus all of our resources on one particular project, we might not be able to do another project concurrently,” Elliot reported. “Using prefabricated bathroom pods reduced our manpower by 30-35 percent and allowed us to spread out our resources and actually do more work.”
Further maximizing the efficiency of available labor, it typically requires three team members to position each pod into its designated space. Within a regular eight-hour shift, approximately 30 pods can be lifted and set into place. It only takes an additional 1-2 hours per pod to execute the full installation process. Fix, who worked specifically on the Atrium Health Pineville-Palmetto Tower, underscored the valuable time-savings. “Prefabrication helped us save one calendar day per bathroom pod,” he said. “We had 108 pods to install, so we saved about three months on the schedule.”
REVOLUTIONIZING FAST-PACED HEALTHCARE CONSTRUCTION WITH PREFABRICATED BATHROOM PODS
SurePods’ expertise in manufacturing bathroom pods helped Atrium Health and the associated design teams successfully execute their vision. "We knew that we could implement this approach really easily if we had the right trade partners with us,” Huneycutt said. “SurePods did a great job because they've been there, done that.” according to Schroder.
“We could not have built these pods on our own and gotten the same quality. Let alone have gotten them on time and at a reasonable price point.”
We Think You'll Like ...
SurePods provided 72 patient bathroom pods for the 5-story Carolinas Rehabilitation Replacement Facility.
SurePods’ approval by HCAI for healthcare facilities in the Golden State marks a milestone for expanding prefabrication capabilities that support all projects.
Prefabricated, modular bathroom pods are revolutionizing healthcare construction by providing a standardized and cost-effective solution. Read about how SurePods products benefit all stakeholders, from architects to end-users.