Case Study
Case Study: Meeting Hospitality Construction Demands with Prefabricated Bathrooms
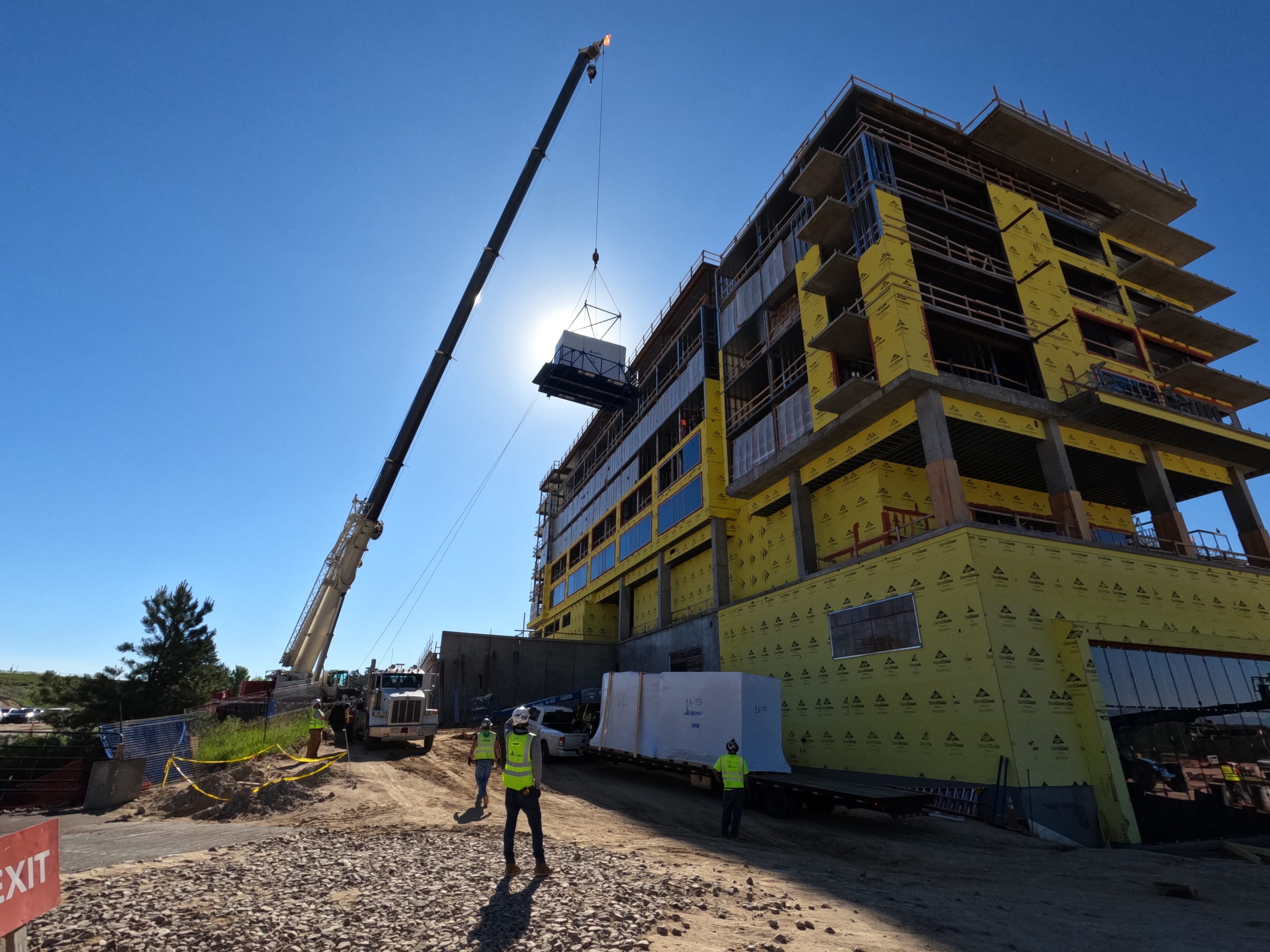
LABOR SHORTAGES, ENVIRONMENTAL CHALLENGES, AND A CONSTRAINED SITE
In luxury hotels, especially in areas like bathrooms, the quality of tile work significantly affects the overall guest experience and the facility's long-term maintenance, making specialized labor such as tile setters critical. With a nationwide shortage of skilled labor, this project endured the same challenge. Moreover, the project spanned four seasons and endured considerable weather impacts. Significant quality issues and schedule delays could have occurred if the general contractor, GE Johnson (a DPR family company), had not recommended a prefab-centric approach that included modular bathroom pods.
You're always going to have issues on the project regardless, and prefab reduces the number of issues, and it allows more flexibility within your schedule to absorb and properly manage other things that get thrown your way.
Additionally, the project's complexity was increased due to constrained site logistics, including limited lay-down space and areas for construction activities. Detailed coordination and planning were required to utilize the tower crane to facilitate loading the bathroom pods into the building.
LEAN CONSTRUCTION PRINCIPLES ADVANCE DESIGN & TIMELY PRODUCTION OF BATHROOM PODS
Bathrooms are among the most resource-intensive parts of a hospitality project. Producing 320-bathroom pods within a controlled environment with out-of-state labor helped alleviate a schedule gap by taking roughly 8 to 12 trades off-site to perform the work concurrently, including the tile work. "Implementing off-site and using labor forces from other regions allowed us to propose a schedule acceleration from the pursuit phase and watch it come to fruition on the project," said Paul Sweeney, GE Johnson’s Director of Prefabrication.
Constructing the pods off-site also decreased the number of quality control issues compared to stick-built bathrooms, which typically require long punch lists and rework due to the number of trades on-site. SurePods' controlled environment allows for thorough 120-point quality assurance inspection and testing, guaranteeing execution of high-end material finishes.
The team experienced a simple installation process described by GE Johnson as a “plug and play” solution. This minimized on-site labor and ensured easy unloading at the job site, alleviating the laydown area of more materials and streamlining overall project management.
The sequence planning determined exactly which bay or window in the building was going to be available so that the pods could be lifted and set.
THE VALUE OF MODULAR BATHROOM PODS
The Hotel Polaris at the United States Air Force Academy project highlighted the advantages of prefabrication in large-scale hospitality projects. By incorporating prefabricated bathroom pods from SurePods, GE Johnson overcame significant labor availability and site coordination challenges, supported the project schedule, and improved overall quality. The project's success was a testament to the effective collaboration between all stakeholders, from initial design through final installation, proving the value of modular construction in meeting modern construction demands.
Labor and schedule were our biggest successes.